CONDITIONNEMENT
Alors que l’heure est à la décarbonation et à l’application du décret « 3R », il peut sembler assez contradictoire de surdimensionner les sacs de produits en vrac. Constatant un manque de solutions techniques sur le marché, CETEC a imaginé un procédé innovant permettant de compacter le produit avant son ensachage, ce qui diminue la génération de poussières et réduit significativement la taille des sacs. Entretien avec Mathias Elie, responsable commercial chez CETEC.
VOS SOLUTIONS EXISTANTES PERMETTAIENT-ELLES DÉJÀ DE RÉDUIRE LES DISPERSIONS DE POUSSIÈRES ?
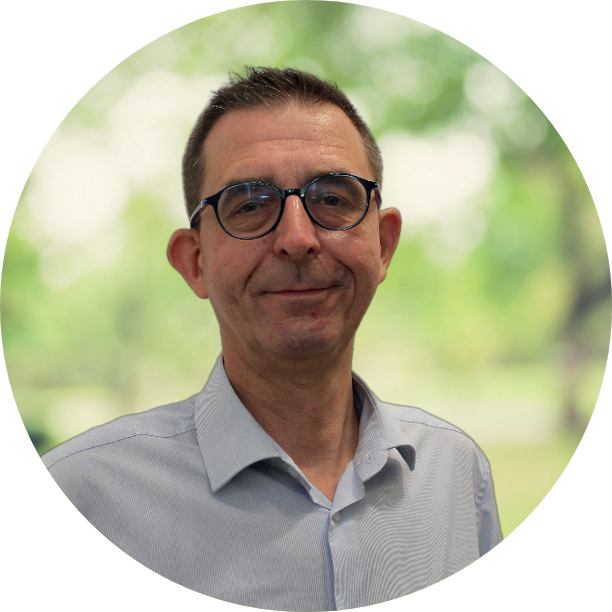
Mathias Elie : Nous avons toujours travaillé sur l’élimination des poussières générées par les process de conditionnement, cela afin de garantir de bonnes cadences. CETEC était déjà fournisseur de solutions pour les sacs de petites dimensions, c’est-à-dire de 2 à 10 kg pour nous, que ce soit dans le secteur des ingrédients ou celui du bâtiment. Nous cherchions à concevoir un procédé plus propre, mais cela nécessitait de fonctionner à des vitesses relativement faibles, en générant encore malheureusement de la poussière. Nous étions obligés d’agrandir les sacs car le produit foisonne à son dosage-remplissage. Une autre technique consiste à doser préalablement dans une benne, au plus haut, puis à accélérer la chute du produit. Celle-ci augmente néanmoins l’effet « splash » et entraîne des nuages de poussière, du foisonnement, des fines, des salissures de sac ou de soudures, etc. L’industriel perd rapidement en conformité produit. CETEC a toujours travaillé sur les différentes technologies, en les améliorant mais tout en gardant à l’esprit qu’elles n’étaient pas parfaites.
COMMENT LE MARCHÉ A-T-IL ÉVOLUÉ EN CE QUI CONCERNE L’ENSACHAGE DE PRODUITS VRAC ?
M. E. : Tout d’abord, il faut garder à l’esprit qu’auparavant le marché ne fournissait que des sacs de 25 kg. Peu à peu, les particuliers se sont mis à consommer des produits conditionnés pour les professionnels, ce qui a créé un nouveau marché. Les industriels ont développé leurs gammes en sacs de 5 à 10 kg et les machines en place devaient répondre à une grande famille de produits divers, qui ne se ressemblent pas. Ces machines sont devenues très compliquées à régler, la solution étant parfois de simplement baisser la cadence. Ensuite, il faut prendre en considération les démarches de décarbonation en France : pour y parvenir, il est nécessaire d’optimiser son process et de modifier ses standards de fabrication. Pour les ingrédients, on cherchera par exemple à broyer ou à mélanger moins, tandis que dans le secteur du bâtiment nous ne sommes plus sur les mêmes conditions de chauffe dans le process de fabrication. Nous nous trouvons alors dans une situation paradoxale : le volume du produit augmente alors que nous cherchons à réduire la taille des sacs dans un objectif de décarbonisation. Le calcul est simple : ce n’est pas possible !
COMMENT L’IDÉE DU JUST’IN BAG VOUS EST-ELLE VENUE ?
M. E. : Cela faisait déjà quelques années que nous avions mis en place des groupes de travail pour trouver des solutions pertinentes. Nous avons mené beaucoup de recherches et, en 2022, l’idée est venue d’un échec rencontré sur des tests de désaération d’un produit chez l’un de nos clients. Sur son installation, la pompe à vide s’est affolée et la canne a aspiré tout le produit : au lieu de désaérer le produit, celui-ci s’est trouvé complètement émotté autour de la canne. C’est justement ce que nous cherchions à faire pour une autre application. En durcissant le produit, nous pouvons finalement le manipuler comme un bloc de produit solide. Nous avons vérifié que le phénomène était reproductible avec différentes poudres et que les mottes ne se désagrégeaient pas. Pour renouveler le procédé, il fallait aussi assurer une phase de décolmatage par micro-vibration et air à contre-courant.
POUVEZ-VOUS DÉTAILLER CHAQUE ÉTAPE DU PROCÉDÉ ?
M. E. : Au départ du process, le produit est stocké dans une trémie vrac qui alimente un doseur à vis en pesée nette. La poudre va être prédosée dans une benne pour viser le poids exact. Ce réceptacle aura la section du sac et une forme pour « gabariser » la dose par rapport à la largeur de sac. Le produit sera moulé dans cette benne. Une canne de vide montée sur un système monte et baisse, et un transfert descendra dans le produit pour le densifier, le désaérer et l’agglomérer. Au signal de dosage, la benne s’ouvre et le produit en motte autour de la canne va être descendu dans le sac. Ensuite, un autre cycle est lancé, avec remontée de la canne, transfert, position haute pour décolmatage en caisson. Le sac est rempli sans poussière et n’a pas besoin d’être vibré ou désaéré. Le Just’In Bag est adapté aux sacs de 5 à 10 kg mais, à terme, nous proposerons une gamme de 2 kg. En cadence, le procédé assure cinq sacs à la minute pour la version Mono, et dix sacs à la minute pour la version Duo.
QUELS SONT LES BÉNÉFICES DIRECTS POUR L’INDUSTRIEL ?
M. E. : Les produits ne cessent de se complexifier, et il fallait apporter une réponse alternative à l’augmentation de la hauteur des sacs due à leur faible largeur. Le procédé Just’In Bag permet de compacter le produit, ce qui apporte deux grands avantages pour l’utilisateur : réduire le niveau de poussière et réduire le volume des produits, donc réduire la dimension des sacs et le poids des emballages. Le gain principal est la diminution de la taille du sac : sa hauteur sera de 20 à 30 % minimum inférieure à la taille des sacs existants. Le gain financier sera direct et la réduction du poids des emballages, recherchée par les distributeurs, mesurable très simplement. Parallèlement, réduire les poussières permet notamment la production plus linéaire des produits, la protection des machines et de l’environnement, et l’amélioration des conditions de travail des opérateurs. Les opérations de maintenance n’en sont que plus réduites. Les industriels peuvent aussi améliorer le sac dans sa conformité, dans sa présentation, dans son traitement et dans son linéaire. Le Just-In Bag est polyvalent et a l’avantage de gérer aussi bien les sacs papier que les sacs plastiques. Il s’agit d’une solution offrant de nombreuses opportunités dans un contexte de décarbonation et de l’application du décret dit « 3R ».
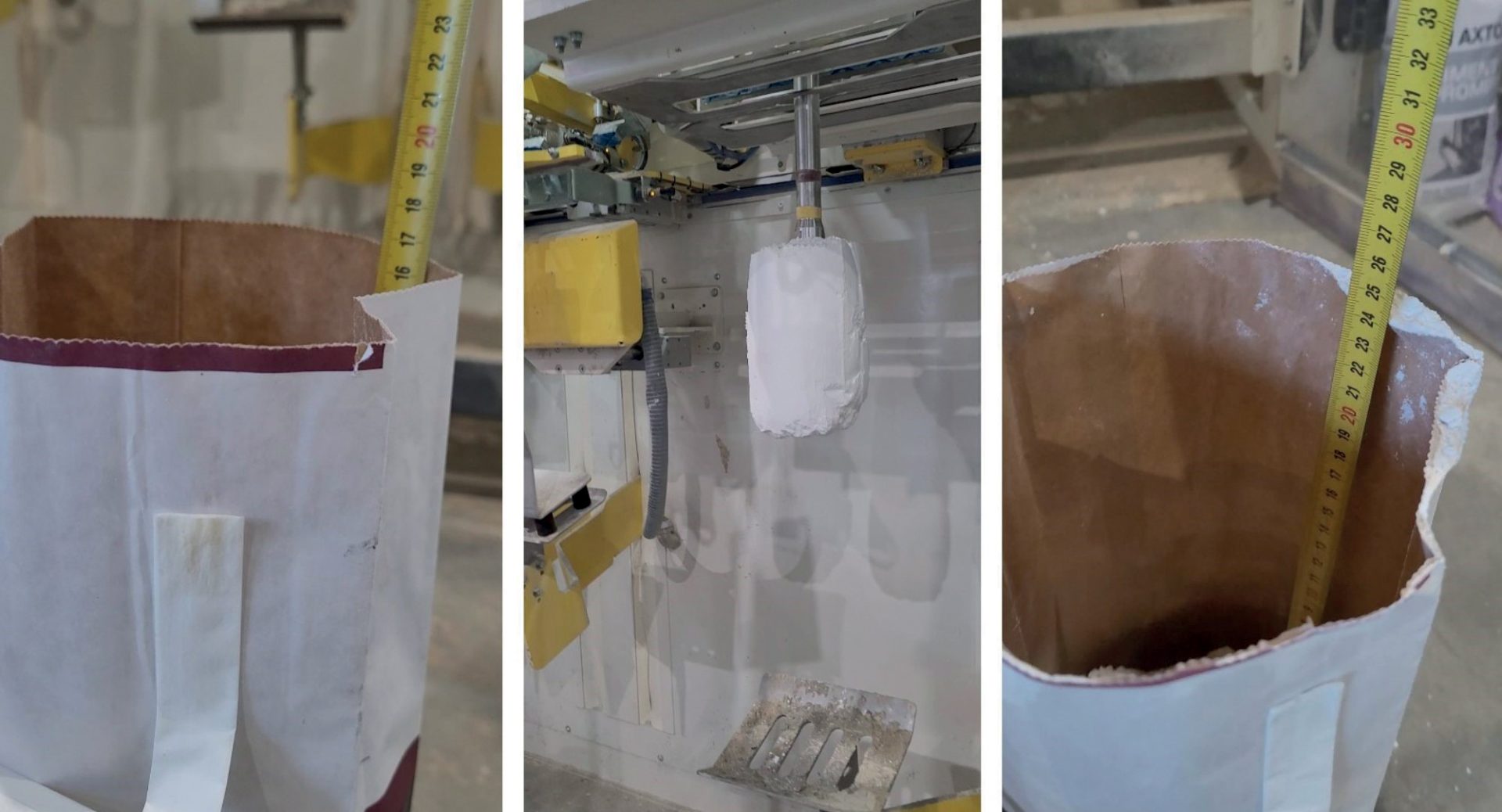
COMMENT SE SONT DÉROULÉS LES PREMIERS ESSAIS ?
M. E. : Nous avons réalisé les premiers tests avec des machines semi-automatiques et des bancs tests. Nous avons ensuite défini des modes de fonctionnement et une étude de conception d’une machine définitive. Pour confirmer nos résultats, nous nous sommes procuré un sac de colle à carrelage existant en linéaire, sans compactage, puis nous l’avons présenté sous la canne d’émottage. Nous avons ensuite motté, puis nous avons retiré le sac avant de le remplir à nouveau pour mesurer l’espace des têtes vides dans le sac. Nous avons constaté un gain de 25 à 30 %, celui-ci pouvant être plus important selon les cas, surtout en sortie de process. Nous sommes en cours de validation de la machine définitive et nous attendons le Factory Acceptance Test (FAT) au 1er semestre 2025 pour lancer les livraisons et les mises en route sur site.
COMMENT L’INDUSTRIEL PEUT-IL ANTICIPER SON RETOUR SUR INVESTISSEMENT ?
M. E. : C’est à lui-même qu’il convient de réaliser les calculs. Il pourra retenir que la protection des équipes opérationnelles, bien que difficile à quantifier, est une priorité. Il pourra également intégrer la plus grande longévité des installations d’ensachage. Aussi, pour une unité moyenne, en réalisant environ 25 % d’économie de taille de sac, il pourrait espérer un gain compris entre 40 000 et 50 000 € par an. D’autres points peuvent être pris en compte d’un point de vue logistique : l’industriel pourra notamment placer davantage de sacs sur ses palettes. Enfin, au-delà du retour sur investissement direct, un sac bien proportionné apporte aussi des avantages indéniables pour le distributeur, qui aura alors un linéaire mieux tenu, davantage de stock en rayon, moins de réassort, etc. Les partenariats n’en seront qu’améliorés. La réduction du poids des emballages apportera aussi des économies dans la filière entre producteurs et distributeurs à l’égard du versement des écotaxes.
LE MARCHÉ EST-IL RÉCEPTIF À CETTE INNOVATION ?
M. E. : Nous avons présenté la solution il y a peu de temps, et les industriels se pressent déjà pour nous rencontrer et découvrir comment le Just’In Bag fonctionne. Ils comprennent rapidement ce phénomène de compactage et qu’il est efficace. Ils savent que cette solution apportera une plus-value à leur process. Nous avons également reçu l’organisme CITEO qui souhaitait découvrir le process : ils ont pu apprécier les efforts et les actes concrets mis en oeuvre pour diminuer la taille des sacs. La réduction des emballages est un sujet clé pour les prochaines années. Nous avons toute une filière auprès de laquelle promotionner notre innovation : industriels, fabricants de sacs, département produit des GSB.
LA TECHNOLOGIE PRIMÉE
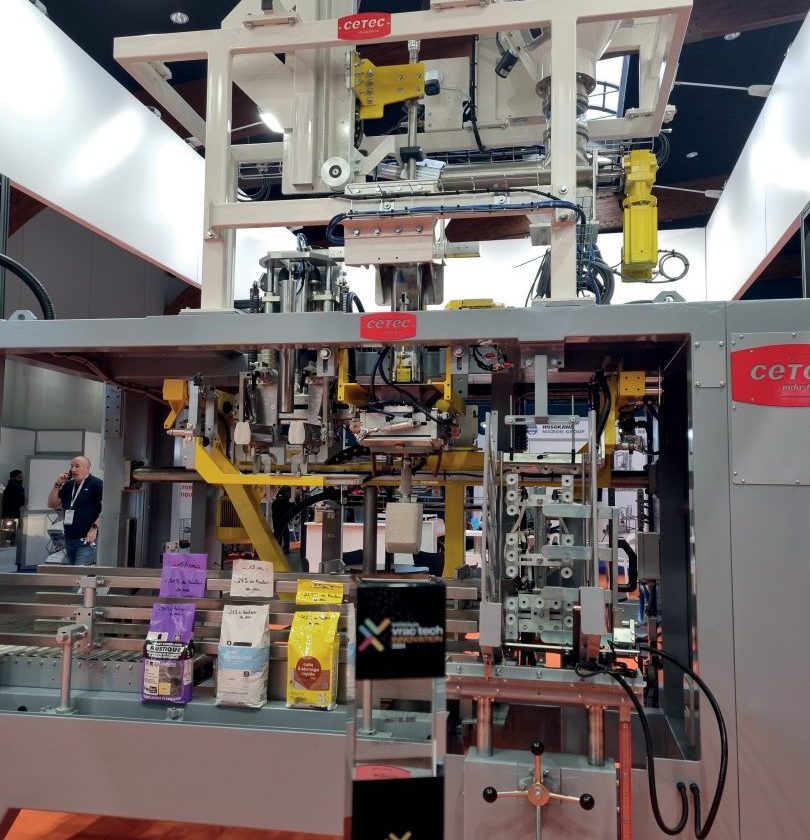
Parmi les quatorze projets en compétition lors du concours VracTech Innovation, trois innovations se sont démarquées et ont été récompensées lors de la remise des prix le 3 décembre 2024, lors du salon Vractech organisé à Mâcon (71). CETEC s’est vu remettre le VracTech d’Or pour sa solution Just’In Bag, le seul équipement en sac à gueule ouverte permettant de compacter le produit avant le remplissage du sac. Regis Labrue, dirigeant de CETEC, témoignait lors de la remise du trophée : « Nous avons créé un module qui permet de désaérer le produit, de le compacter et de le déposer au fond du sac, sans poussière et avec un volume minimal. Le produit étant aggloméré autour de la canne, il n’émet plus de poussière. Grâce à de nombreux essais, le Just’In Bag permet de diminuer la taille du sac de 20 à 40 %. »D’UN VRACTECH D’OR