Transfert & Dosage
Parmi les diverses normes et réglementations qui encadrent les activités de l'industrie alimentaire, l'ATEX est à la fois la plus commentée et la moins bien appliquée. De l'analyse du risque à la solution technique, subsistent souvent des interrogations et des discours parfois discordants entre les industriels et leurs fournisseurs. Analyse de Thierry Carbonell, conseiller ATEX pour APIA Technologie.
Dès 2005, APIA Technologie a fait le choix d’intégrer un conseiller ATEX dans son organisation. Le spécialiste du dosage et du transfert des poudres pour l’agroalimentaire démystifie cette réglementation et nous partage sa démarche pragmatique et appliquée aux équipements. Que faut-il en savoir ? Quelles conséquences sur les process et les équipements ? À quels coûts ? Voici les réponses aux questions fréquemment soulevées par les responsables de sites industriels.
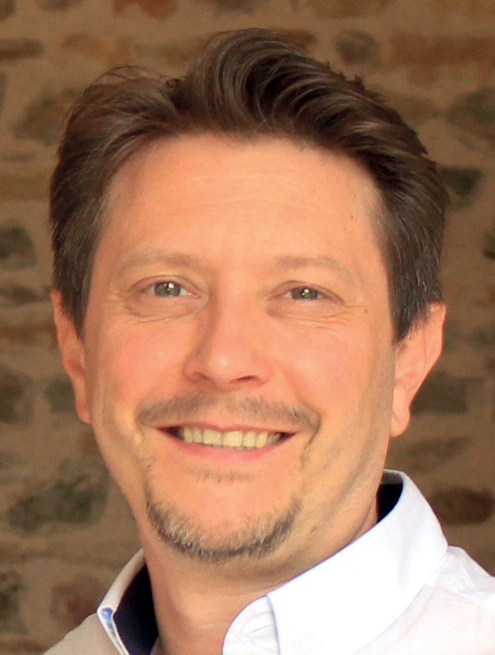
L’ATEX DANS LES USINES ALIMENTAIRES : QUE FAUT-IL RETENIR ?
Le cadre
Il est bon d'écarter d'abord l'utilisation de la terminologie « normes ATEX ». Le risque explosif est en réalité encadré par deux directives européennes ATEX :
- Directive 1999/92/CE, transposée en droit français dans le Code du travail : pour les utilisateurs (les industriels qui exploitent les équipements) ;
- Directive 2014/34/UE, transposée en droit français dans le Code de l'environnement : pour les constructeurs (les concepteurs-fabricants des équipements).
La nuance est importante car elle explique bien des incompréhensions entre industriels pas toujours bien informés sur leurs obligations, et fournisseurs parfois ambigus sur les caractéristiques de leurs matériels. En effet, contrairement à une norme, une directive se contente d’imposer des résultats à atteindre, sans imposer les moyens à mettre en place, ce qui laisse de la place aux interprétations.
Pourquoi l’industrie agroalimentaire est-elle concernée ?
Rappelons tout d’abord que les règles ATEX visent à éviter les explosions dans les sites industriels ou, en dernier recours, à en minimiser les conséquences. Elles s’appliquent donc dans tout atelier où sont rassemblées les conditions d’une atmosphère explosive telles que décrites par l’Ineris (expert public pour la maîtrise de risques industriels), aux premiers rangs desquelles :
- La présence d'un combustible dans l'air (matière inflammable) ;
- La présence d'un déclencheur potentiel de la combustion (chaleur ou étincelle).
Parmi les matières inflammables, les carburants ou gaz sont intuitivement identifiés. Il existe cependant une autre source potentielle d’explosion : les poudres, les fines et les poussières en suspension dans l’air. De manière concrète et appliquée : sucre, farine, amidon, céréales, café, poudre de lait, etc. Tous les pulvérulents en général constituent un danger d’inflammation ou d’explosion potentielle qu’il est nécessaire d’évaluer. Ce risque explosif est notamment avéré si des équipements générant chaleur ou étincelles sont en contact avec des matières inflammables : un moteur de machine en surchauffe à cause d’un bourrage matière, de l’électricité statique, une particule métallique embarquée dans le process, etc. Selon le rapport 2019 du site dustsafetyscience.com, les poussières agroalimentaires sont à l’origine de plus de 40 % des explosions industrielles.
Quelles sont les responsabilités de l'exploitant et du constructeur ?
Tout commence par l’identification du risque : est-on en présence d’une atmosphère explosive, quelles sont les zones de l’usine concernées ? Ensuite intervient le choix des équipements adaptés. Le périmètre de responsabilités des uns et des autres est en réalité très clair. Il incombe aux industriels donneurs d’ordre de fournir l’étude de risques sous la forme du Document relatif à la protection contre les explosions. Il est de la responsabilité des fournisseurs de concevoir l’installation qui répond au cahier des charges découlant de l’étude de risque. S’il livre des équipements ATEX, il est tenu de fournir une déclaration UE de conformité (zones 21 et 22) et une attestation d’examen UE de type par un organisme extérieur (zone 20).
Ce qu’il faut retenir :
- Il est de la responsabilité de l’exploitant de déterminer le matériel et les équipements de protection nécessaires pour assurer la sécurité des salariés, et d’en assurer la maintenance ;
- Il est de la responsabilité du fournisseur d’équipements de livrer les matériels conformes au cahier des charges en général, et à la directive ATEX en particulier.
Le zonage ATEX
Tout commence par un état des lieux. Concrètement : le responsable du site industriel dresse l’inventaire des risques, met en place des mesures de prévention, délimite et caractérise les zones sensibles. C’est ce que l’on appelle le zonage ATEX, selon trois niveaux de risque :
- Présence permanente de poussières : zone 20 ;
- Présence occasionnelle de poussières : zone 21 ;
- Présence rare de poussières : zone 22 ;
Cette étape de classement des zones à risque est la plus technique. L’analyse des caractéristiques d’explosivité des poudres est, en particulier, trop souvent négligée. Il est recommandé aux responsables sécurité de se faire accompagner par des bureaux d’études spécialisés. En effet, la sous-évaluation du risque met la vie d’hommes et de femmes en danger : la surévaluation du risque est onéreuse.
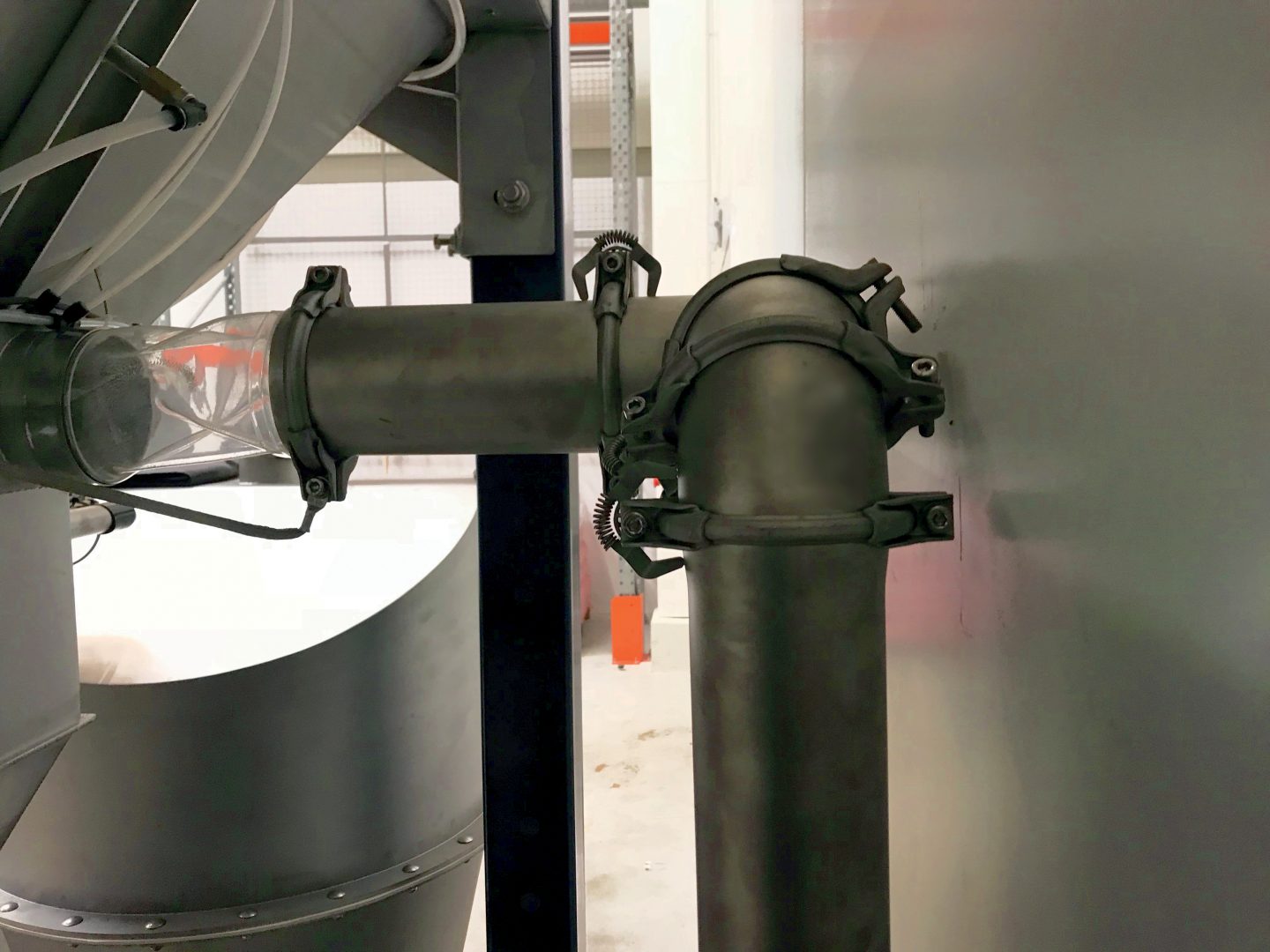
COMMENT CHOISIR LES ÉQUIPEMENTS DE TRANSFERT DE POUDRES ?
Ne pas surévaluer le risque
Faute d’information, et selon le fameux principe de précaution, il n’est pas rare que la décision soit prise de prévoir une installation ATEX sans réelle justification avec les surcoûts qui vont avec. De même, le classement hâtif d’un atelier en zone ATEX génère des coûts souvent sous-estimés. En effet, des mesures de protection variées doivent être instaurées, des plans d’actions mis en place et le personnel régulièrement formé. L’équation consiste donc à éviter des dépenses non indispensables dans une logique de rentabilité, sans jamais déroger à la protection des travailleurs, des biens et de l’environnement.
Bien menée, l’analyse des risques ATEX évitera des zonages ATEX non nécessaires et caractérisera correctement le niveau de risque (zones 20, 21 ou 22).
Des mesures pour éviter un classement en zone ATEX
Avant d’établir le zonage définitif d’un site de production, des mesures de prévention et quelques modifications du process peuvent abaisser le niveau de risque à moindre coût. Il est ainsi possible d’agir sur les sources d’inflammation, comme une température ambiante trop élevée. Pour limiter la présence de matière inflammable dans l’atmosphère, l’installation de systèmes de dépoussiérage s’avère très efficace. La gestion des flux d’ingrédients secs dans une usine agroalimentaire impacte ainsi directement le risque d’explosion. Un transport des poudres en milieu clos et la mise en place de système de dépoussiérage limiteront, par exemple, la production de fines. Et cela peut générer beaucoup d’économies.
Trois catégories de certification ATEX pour répondre aux trois niveaux de risques
Le fabricant de matériel ATEX s’engage à concevoir et fabriquer des appareils qui répondent aux exigences en fonction du zonage ATEX, conformément à la directive ATEX constructeur. APIA Technologie sensibilise ses clients industriels sur l’importance d’exiger les certifications ATEX de leurs partenaires. Des équipements similaires peuvent en réalité présenter des différences de conception et de sécurité majeures mais peu visibles. Le marquage CE sur l’équipement et le certificat font foi. La directive ATEX constructeur prévoit trois catégories de matériels. À chaque catégorie correspond un niveau d’engagement du fabricant :
- Simple contrôle interne pour la catégorie 3D compatibles zone 22 ;
- Contrôle interne avec dépôt d'un dossier auprès d'un organisme notifié pour la catégorie 2D compatible zones 21 et 22 ;
- Attestation d’examen de type par un organisme extérieur avec audits annuels du Système d'assurance qualité pour la catégorie 1D compatible zones 20, 21 et 202.
![]() |
![]() |
L’ENGAGEMENT D’APIA TECHNOLOGIE
L’ATEX, une préoccupation de longue date
Dès 2005, APIA Technologie intègre la problématique ATEX dans le développement de ses solutions de transfert des poudres. Très concrètement, l’objectif est d’obtenir la certification la plus exigeante sur ses systèmes Transitube®. Les premiers essais sont réalisés, suivis de nombreux tests internes et en laboratoire. Enfin, les matériels sont soumis à l’expertise de l’Ineris afin d’obtenir une autorisation de mise sur le marché en catégorie 1. C’est chose faite en 2007. Depuis cette date, le système d’assurance qualité en place dans les ateliers permet de reconduire cette certification année après année.
Accompagner les industriels
Selon APIA Technologie, le rôle du fournisseur est de sensibiliser les industriels aux bonnes pratiques d’une démarche ATEX, sans se substituer à l’exploitant du site, seul responsable de l’évaluation des risques. Les équipes sont régulièrement formées par des intervenants de l’Ineris et peuvent faire appel au conseiller ATEX, référent les questionnements plus pointus qu’ils soient d’ordre sécuritaire, technique ou même juridique. Intervenant dans les sites de production agroalimentaires depuis 30 ans, les experts APIA Technologie sont par ailleurs en mesure de préconiser tous les équipements de mise en conformité ATEX des installations : pièges magnétiques, égrugeonneurs, systèmes anti-bourrage, mise à la terre, etc.
Application des directives aux niveaux national et international
En la personne de Thierry Carbonell, son référent ATEX, APIA Technologie participe aux réunions du CLATEX, le Comité de liaison des équipements ATEX. Les entreprises françaises les plus investies à l’égard des directives risques ATEX s’y retrouvent pour traiter des problématiques terrains et assurer la liaison avec la Communauté européenne. Ce comité prépare également les évolutions à venir, comme la mise en place de la nouvelle norme internationale IECEx qui concerne les matériels électrotechniques. Comme toujours en matière de réglementations, il est question d’harmonisation et de simplification. L’objectif étant que le niveau de qualité et de sécurité exigé ne prenne pas le pas sur le développement technique et qu’il soit accessible aux pays en voie de développement qui négligent encore trop l’aspect sécuritaire.
CONCLUSION
Les directives ATEX sont souvent subies comme un cadre réglementaire de plus, avec son lot de contraintes. N'oublions pas qu'elles sauvent cependant des vies. D'autre part, comme souvent dans le cadre d'une mise en conformité d'un site de production, la réflexion sur la stratégie ATEX au sein d'un site agroalimentaire déclenche un cercle vertueux : qualité, hygiène, diminution de la pénibilité, réduction des coûts d'exploitation.